動力電池雙層板焊接機定制方案
動力電池雙層板焊接機定制方案
為滿足貴司動力電池生產(chǎn)中雙層極板(如正負極集流體、多層匯流排等)高精度、高效率、高一致性的焊接需求,特制定本定制化焊接機方案,旨在提供可靠的生產(chǎn)利器。
一、核心需求與挑戰(zhàn)分析
工件特性: 雙層薄板(常為鋁/銅或異種金屬),厚度通常在0.3-1.5mm,要求無飛濺、熔深可控、低熱變形。
工藝要求: 高精度定位(±0.1mm),高速焊接(多焊點/連續(xù)縫),優(yōu)異的一致性(CPK≥1.33),焊點/焊縫強度滿足拉伸測試。
核心挑戰(zhàn): 層間貼合度影響熱傳導(dǎo)、異種金屬焊接界面控制、薄板易變形、高速下的精度保持。
二、定制化設(shè)備方案設(shè)計
1. 高精度定位與夾持系統(tǒng):
精密載具: 針對雙層板結(jié)構(gòu)定制化設(shè)計真空吸附或精密機械夾持工裝,確保層間緊密貼合無間隙,減少焊接缺陷。
視覺定位系統(tǒng): 集成高分辨率CCD相機與圖像處理軟件,實現(xiàn)焊前特征點自動識別與位置補償(精度±0.05mm),適應(yīng)來料微小偏差。
高剛性運動平臺: 采用直線電機或高精度絲杠模組,重復(fù)定位精度≤±0.02mm,確保焊接路徑精確執(zhí)行。
2. 先進焊接工藝與執(zhí)行單元:
激光源選擇: 推薦高光束質(zhì)量光纖激光器(如IPG/YLS,功率范圍1.5-3kW),能量穩(wěn)定、調(diào)制響應(yīng)快,適用于薄板精密焊接。
焊接頭配置: 定制準直/聚焦光學系統(tǒng),搭配高速振鏡(掃描速度≥10m/s),實現(xiàn)多點同步焊、復(fù)雜軌跡焊接,大幅提升效率。
工藝優(yōu)化: 采用調(diào)制波形控制技術(shù)(如脈沖/連續(xù)波形可調(diào)),精確控制熱輸入,抑制飛濺;對異種金屬焊接,應(yīng)用擺動焊接或特殊波形優(yōu)化熔池混合,保證界面強度;配備同軸保護氣(Ar/N2混合氣)系統(tǒng),防止氧化。
3. 智能過程監(jiān)控與質(zhì)量保障:
實時熔深監(jiān)測: 集成PLASMA/背反射光傳感器,實時監(jiān)測焊接狀態(tài),異常即時報警或調(diào)整參數(shù)。
焊接后視覺檢測: 配置第二套視覺系統(tǒng),自動檢測焊點位置、尺寸、表面缺陷(凹坑、裂紋、爆點),實現(xiàn)100%焊后外觀質(zhì)檢。
數(shù)據(jù)追溯系統(tǒng): 完整記錄焊接參數(shù)(功率、速度、波形)、定位數(shù)據(jù)、檢測結(jié)果,綁定電池單體/模組ID,滿足可追溯性要求。
4. 高效自動化集成:
雙工位設(shè)計: 上料/焊接/下料并行,設(shè)備稼動率提升30%以上。
模塊化結(jié)構(gòu): 便于維護保養(yǎng),關(guān)鍵部件(激光器、振鏡)快拆設(shè)計。
人機界面: 配備10英寸以上HMI觸摸屏,支持配方管理、參數(shù)設(shè)置、生產(chǎn)報表、故障診斷。
三、核心優(yōu)勢與價值
精度保障: 視覺定位+高剛性運動平臺,解決雙層板對位難題,良品率≥99.5%。
效率提升: 振鏡高速掃描+雙工位,焊接節(jié)拍較傳統(tǒng)方案提升40%-60%。
質(zhì)量穩(wěn)定: 閉環(huán)工藝控制+實時監(jiān)測+焊后AI質(zhì)檢,確保CPK≥1.67。
柔性生產(chǎn): 通過配方切換,快速適應(yīng)不同尺寸、形狀的雙層板焊接需求。
智能管理: 全面數(shù)據(jù)追溯,為工藝優(yōu)化與質(zhì)量控制提供堅實依據(jù)。
四、實施與服務(wù)
深度協(xié)同: 前期進行焊接試樣與工藝驗證,確保設(shè)備參數(shù)完美匹配產(chǎn)品。
交鑰匙交付: 包含設(shè)備安裝、調(diào)試、工藝驗證、操作培訓(xùn)及完整文檔。
持續(xù)支持: 提供遠程診斷、快速響應(yīng)維護及工藝升級服務(wù)。
五、總結(jié)
本定制化雙層板焊接機方案,深度融合精密機械、智能視覺、先進激光工藝與數(shù)字監(jiān)控技術(shù),針對性解決動力電池雙層板焊接的核心痛點,為貴司提供高可靠、高效率、高智能的焊接解決方案,助力提升電池生產(chǎn)質(zhì)量與市場競爭力。
> 方案特點:聚焦精度、效率、質(zhì)量,以定制化解雙層焊接難題,數(shù)據(jù)驅(qū)動智能生產(chǎn)。
點擊右側(cè)按鈕,了解更多激光打標機報價方案。
相關(guān)推薦
動力電池雙層板焊接機定制方案設(shè)計
動力電池雙層板焊接機定制方案設(shè)計
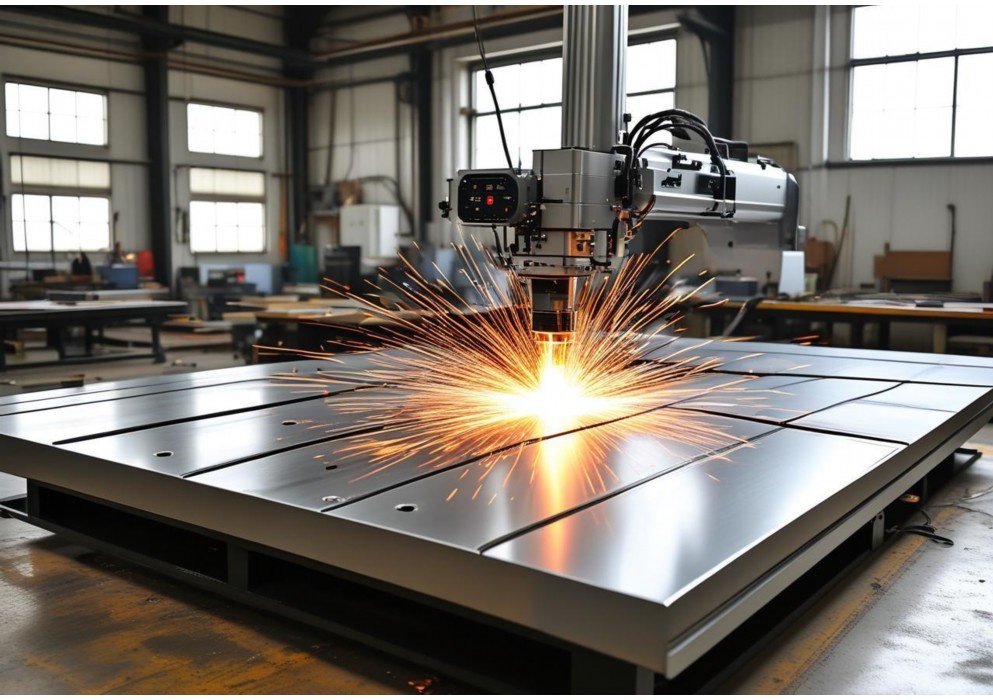
動力電池雙層板焊接機定制方案設(shè)計
一、 項目背景與需求分析
動力電池模組中,雙層電極板(如Busbar、極耳與連接片的層疊結(jié)構(gòu))的可靠焊接是確保電池組導(dǎo)電性、機械強度與安全性的核心工藝。為滿足高精度、高效率、高一致性的生產(chǎn)要求,特設(shè)計此定制化雙層板焊接機方案,解決傳統(tǒng)設(shè)備存在的定位不準、熱影響區(qū)大、效率低下等問題。
二、 核心設(shè)計目標
1. 高精度焊接:定位精度≤±0.05mm,焊縫寬度誤差≤±5%。
2. 零飛濺與低熱輸入:抑制焊接飛濺(飛濺率<3%),減少熱影響區(qū),避免損傷電芯。 3. 高效生產(chǎn):節(jié)拍時間≤8秒/焊點(雙工位設(shè)計),支持24小時連續(xù)運行。 4. 強兼容性:適配0.3~2.0mm銅/鋁板及鎳片疊焊,支持矩形、異形焊點。 5. 智能質(zhì)量管控:集成在線檢測(焊后電阻、外觀AI視覺),數(shù)據(jù)實時追溯。 三、 定制化技術(shù)方案 1. 設(shè)備結(jié)構(gòu)與運動系統(tǒng): 雙工位旋轉(zhuǎn)平臺:上料/焊接與下料/檢測同步進行,提升設(shè)備綜合效率(OEE)。 高剛性龍門架:搭載直線電機驅(qū)動,實現(xiàn)焊接頭XY方向±0.01mm重復(fù)定位精度。 精密伺服壓緊機構(gòu):分層獨立加壓(壓力可控范圍50~500N),確保層間緊密貼合,消除虛焊。 2. 焊接工藝系統(tǒng): 定制高頻逆變激光器:光纖激光(波長1070nm)或藍光激光(針對高反材料),功率0~6kW連續(xù)可調(diào),配備同軸保護氣簾。 智能焊接頭:集成CCD視覺定位、紅外測溫、焊縫跟蹤(LWM),實時調(diào)節(jié)功率與焦距。 工藝專家數(shù)據(jù)庫:預(yù)置銅鋁異種材料焊接、薄板疊焊等工藝包,支持波形調(diào)制(PWM/PFM)抑制飛濺。 3. 智能控制系統(tǒng): 多軸運動控制卡:基于EtherCAT總線,實現(xiàn)激光-運動-壓力多參數(shù)協(xié)同控制。 機器視覺系統(tǒng):焊前定位(糾偏±0.5mm)、焊中熔池監(jiān)控、焊后缺陷檢測(氣孔、裂紋識別率>99%)。
MES接口:焊接參數(shù)(功率、速度、溫度曲線)、質(zhì)量數(shù)據(jù)(電阻值、缺陷圖片)上傳至工廠管理系統(tǒng)。
四、 關(guān)鍵優(yōu)勢
質(zhì)量提升:分層加壓+激光波形控制,實現(xiàn)無飛濺深熔焊,良率≥99.5%。
成本優(yōu)化:雙工位設(shè)計降低單點焊接成本,設(shè)備能耗降低15%(對比傳統(tǒng)振鏡焊)。
快速換型:配方管理系統(tǒng)支持1分鐘內(nèi)切換產(chǎn)品程序,適應(yīng)多型號電池生產(chǎn)。
智能運維:預(yù)測性維護系統(tǒng)監(jiān)控激光器壽命、光學鏡片污染度,減少非計劃停機。
五、 實施計劃
1. 需求細化(2周):確認工件圖紙、節(jié)拍目標、車間環(huán)境。
2. 設(shè)計評審(3周):完成3D方案、電氣原理圖、風險分析(FMEA)。
3. 制造與測試(14周):裝配、單模塊調(diào)試、整機聯(lián)調(diào)(焊接工藝驗證)。
4. 交付與培訓(xùn)(2周):FAT驗收、現(xiàn)場安裝、操作/維護培訓(xùn)。
六、 服務(wù)保障
提供2年核心部件質(zhì)保,終身技術(shù)支持,遠程診斷系統(tǒng)實時響應(yīng),定期工藝優(yōu)化服務(wù)。
方案價值:本定制設(shè)備通過分層精準控壓、激光-視覺閉環(huán)控制、雙工位并行作業(yè)三大核心設(shè)計,攻克了雙層板焊接的定位與熱管理難題,顯著提升電池模組的安全性與生產(chǎn)效率,為動力電池大規(guī)模智能制造提供可靠裝備支撐。
點擊右側(cè)按鈕,了解更多激光打標機報價方案。
動力電池雙層板焊接機定制方案及流程
動力電池雙層板焊接機定制方案及流程
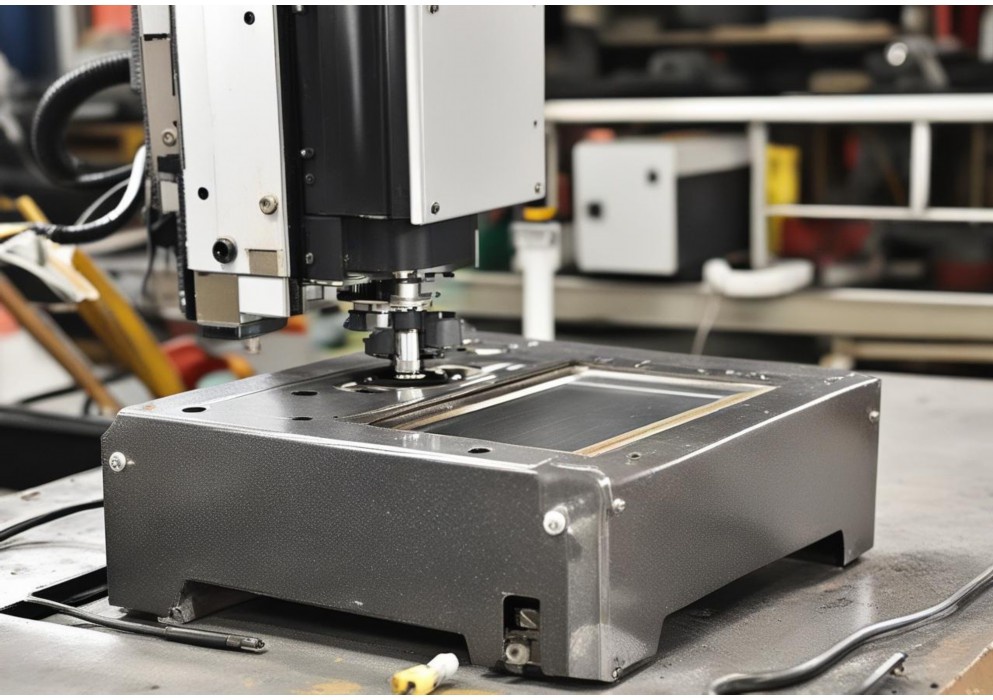
以下是為您定制的動力電池雙層板焊接機方案及流程(約800字):
動力電池雙層板焊接機定制方案
一、項目需求分析
1. 焊接對象:動力電池鋁/銅雙層極耳、蓋板與極柱組合
2. 核心要求:
– 焊接精度:±0.1mm
– 焊接速度:≥1.5秒/點
– 良率目標:≥99.8%
– 兼容性:支持3種以上電池型號(需用戶提供尺寸范圍)
二、設(shè)備核心配置
“`mermaid
graph LR
A[激光焊接系統(tǒng)] –> B[500W光纖激光器]
A –> C[振鏡掃描系統(tǒng)]
D[精密定位系統(tǒng)] –> E[伺服電機+直線導(dǎo)軌]
D –> F[CCD視覺定位]
G[控制系統(tǒng)] –> H[PLC+工控機]
G –> I[人機交互界面]
“`
三、定制化設(shè)計要點
1. 焊接工藝優(yōu)化:
– 采用波形調(diào)制技術(shù),解決鋁銅異種金屬焊接脆性問題
– 雙層板間隙自動補償(0-0.3mm自適應(yīng))
2. 專用夾具系統(tǒng):
– 模塊化設(shè)計,支持快速換型(換型時間≤5min)
– 氣動夾持+真空吸附雙保險
3. 質(zhì)量監(jiān)控系統(tǒng):
– 實時熔深監(jiān)測(紅外測溫+等離子監(jiān)測)
– 每焊點生成數(shù)據(jù)追溯碼
四、定制開發(fā)流程
“`mermaid
graph TD
S1[需求確認] –> S2[概念設(shè)計評審]
S2 –> S3[機械/電氣設(shè)計]
S3 –> S4[模塊化組裝]
S4 –> S5[工藝參數(shù)調(diào)試]
S5 –> S6[72小時連續(xù)測試]
S6 –> S7[客戶現(xiàn)場驗收]
“`
五、關(guān)鍵節(jié)點說明
1. 設(shè)計階段(4周):
– 完成3D布局圖評審
– 確定傳感器選型(基恩士/康耐視)
2. 制造階段(8周):
– 機架加工(航空鋁型材)
– 德國進口直線模組組裝
3. 調(diào)試階段(2周):
– 焊接參數(shù)庫建立(功率/頻率/離焦量組合測試)
– 設(shè)計DOE實驗驗證焊接強度(>15MPa)
4. 交付階段(1周):
– 提供操作培訓(xùn)視頻
– 交付備件清單(激光保護鏡片/陶瓷體等)
六、技術(shù)保障措施
– 防爆設(shè)計:焊接倉氮氣吹掃+IP54防護
– 誤操作防護:雙安全光柵+急?;芈?/p>
– 維護性:關(guān)鍵部件快拆設(shè)計(更換振鏡≤30min)
七、增值服務(wù)
1. 提供焊接工藝認證報告(IEC 62619標準)
2. 預(yù)留MES系統(tǒng)接口(支持OPC UA協(xié)議)
3. 首年免費遠程診斷服務(wù)
方案優(yōu)勢總結(jié)
1. 效率提升:較傳統(tǒng)焊接機節(jié)拍縮短40%
2. 成本控制:模塊化設(shè)計降低后期改造成本
3. 質(zhì)量保障:閉環(huán)監(jiān)控系統(tǒng)杜絕漏焊/虛焊
4. 擴展能力:預(yù)留第3層擴展工位接口
> 執(zhí)行提示:建議用戶提前準備3組典型樣品用于工藝開發(fā),并提供車間布局圖(含壓縮空氣/電力接口位置)。整機交付周期約14周,首批工藝驗證需用戶參與參數(shù)確認。
本方案已整合行業(yè)痛點解決方案,具體參數(shù)可根據(jù)實際需求微調(diào)。需要設(shè)備布局圖或焊接樣品測試報告可進一步提供。
點擊右側(cè)按鈕,了解更多激光打標機報價方案。
燃料電池雙極板焊接
燃料電池雙極板焊接
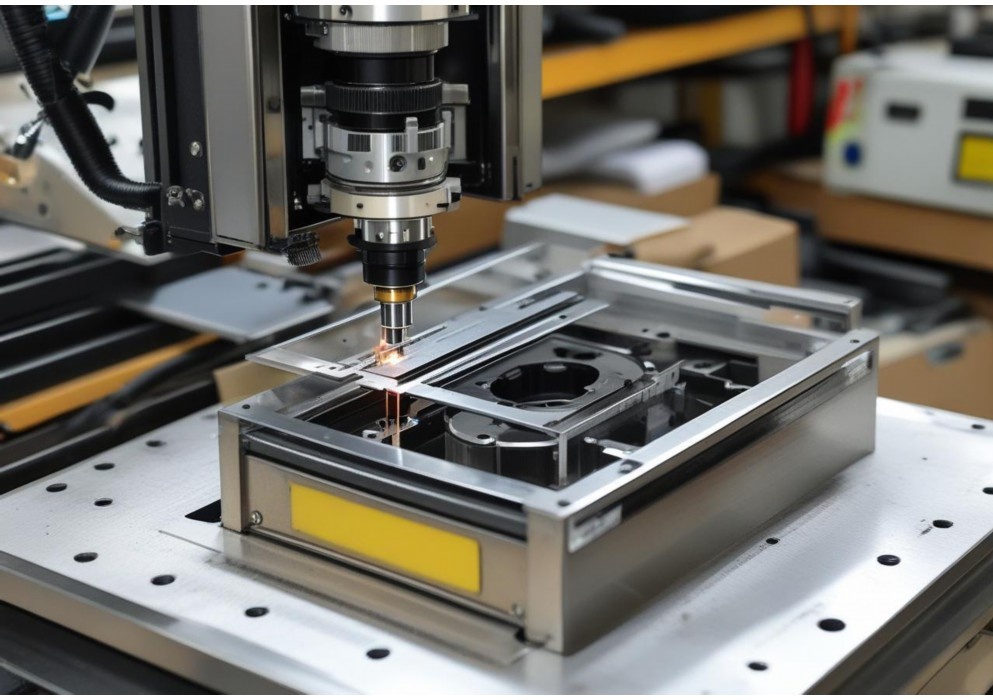
燃料電池雙極板焊接:精密連接的藝術(shù)與挑戰(zhàn)
在燃料電池這座精密的“能量工廠”中,雙極板(BPP)如同不可或缺的“骨架”與“血脈網(wǎng)絡(luò)”。它承載著多重使命:分隔氫氧反應(yīng)氣體、收集傳導(dǎo)電流、支撐膜電極組件、并借助內(nèi)部精細流道確保反應(yīng)物均勻分布與產(chǎn)物高效排出。而將兩塊單極板(陽極板與陰極板)或單極板與密封元件可靠連接成整體的焊接工藝,直接決定了電池堆的密封性、導(dǎo)電性、結(jié)構(gòu)強度與長期壽命,堪稱燃料電池制造中的核心技術(shù)堡壘。
一、 焊接難點:苛刻要求下的精密挑戰(zhàn)
雙極板焊接面臨著一系列獨特且苛刻的技術(shù)挑戰(zhàn),使其成為制造工藝中的關(guān)鍵瓶頸:
1. 材料敏感性:
不銹鋼板: 常用材料(如316L)雖具備良好強度與耐蝕性,但在焊接高溫下易發(fā)生熱變形、晶粒粗化,導(dǎo)致導(dǎo)電性下降和殘余應(yīng)力累積,影響長期密封可靠性。
石墨/復(fù)合材料板: 脆性材料對熱輸入極其敏感,極易產(chǎn)生裂紋甚至破碎,傳統(tǒng)熔焊幾乎不可行。
鈦合金板: 高溫下易與大氣中的氧、氮發(fā)生反應(yīng),形成脆性化合物,需嚴格惰性氣體保護。
2. 極致的密封要求: 氫氣的微小分子特性使得任何細微泄漏都不可接受。焊接必須形成連續(xù)、致密、無缺陷的密封線,確保反應(yīng)氣體(H?, O?/空氣)與冷卻液在高壓下嚴格隔離,杜絕互竄。
3. 導(dǎo)電性保障: 焊接接頭本身必須具有極低的接觸電阻,任何焊接缺陷(如氣孔、未熔合)或氧化層都會顯著增加電阻,導(dǎo)致電池堆內(nèi)阻上升、效率下降和局部過熱。
4. 微變形控制: 雙極板通常輕薄(厚度常<2mm),流道結(jié)構(gòu)精密。焊接熱輸入極易引起翹曲、波浪變形(需控制在<0.1mm級別),影響電池堆的均勻壓緊,導(dǎo)致接觸不良、密封失效甚至損壞膜電極(MEA)。 5. 效率與成本: 雙極板數(shù)量眾多(一個電堆可達數(shù)百片),焊接過程必須高效、穩(wěn)定、自動化程度高,以滿足規(guī)?;a(chǎn)需求并控制成本。 二、 主流焊接技術(shù):各顯其能的解決方案 針對上述挑戰(zhàn),多種先進焊接技術(shù)被應(yīng)用于雙極板制造: 1. 激光焊接: 原理: 利用高能量密度激光束局部熔化材料實現(xiàn)連接。 優(yōu)勢: 能量高度集中、熱影響區(qū)極小、變形小、速度快、精度高、易于自動化。特別適用于不銹鋼和涂層金屬板的深熔焊或精密縫焊/點焊。 挑戰(zhàn): 對裝配間隙要求極為苛刻(常需<0.05mm),參數(shù)控制不當易產(chǎn)生氣孔、飛濺;設(shè)備成本高;焊接鈦合金時需真空或超高純惰性氣體保護。 2. 電阻焊: 原理: 利用電流通過工件接觸面及鄰近區(qū)域產(chǎn)生的電阻熱進行焊接,主要為電阻點焊和縫焊。 優(yōu)勢: 效率高、成本較低、易于實現(xiàn)高速自動化生產(chǎn),尤其適合大批量金屬板點焊連接(如連接兩片單板形成冷卻腔)。 挑戰(zhàn): 產(chǎn)生較大熱變形和壓痕,影響表面平整度和流道功能;接頭為搭接,可能增加接觸電阻;對多層復(fù)雜結(jié)構(gòu)焊接能力有限。 3. 固態(tài)焊接(超聲波焊接): 原理: 利用高頻振動能在壓力下使材料接觸面產(chǎn)生塑性變形和摩擦熱,實現(xiàn)原子間結(jié)合。 優(yōu)勢: 無需熔化、熱輸入極低、無熱變形、無金屬飛濺、節(jié)能、可焊接異種金屬(如金屬與涂層)及部分非金屬復(fù)合材料。 挑戰(zhàn): 通常限于搭接焊點或短縫焊,難以實現(xiàn)長距離連續(xù)密封焊;對工件表面清潔度要求高;焊頭設(shè)計和磨損是問題;對厚板或高強材料能力有限。 三、 質(zhì)量守護:嚴苛檢測不可或缺 焊接質(zhì)量直接關(guān)乎電堆成敗,因此必須實施嚴格的無損檢測: 氦質(zhì)譜檢漏: 高靈敏度檢測焊接密封線的微小泄漏,是保證氣密性的金標準。 X射線檢測: 透視檢查焊縫內(nèi)部缺陷,如氣孔、裂紋、未熔合。 外觀檢查與尺寸測量: 利用光學顯微鏡、三維掃描儀等檢查焊縫形貌、表面缺陷(飛濺、凹陷、裂紋)和工件整體變形量。 導(dǎo)電性測試: 測量焊縫區(qū)域的接觸電阻。 展望:持續(xù)精進,賦能未來 燃料電池產(chǎn)業(yè)的蓬勃發(fā)展對雙極板焊接技術(shù)提出了更高要求:更快的速度、更低的成本、更高的可靠性與一致性,以及對新型材料(如超薄金屬、復(fù)合材料)更好的適應(yīng)性。未來研究將持續(xù)聚焦: 工藝優(yōu)化與智能控制: 利用傳感技術(shù)、人工智能和大數(shù)據(jù)實現(xiàn)焊接過程的實時監(jiān)測、閉環(huán)控制和自適應(yīng)調(diào)整。 新型焊接技術(shù)探索: 如激光-電弧復(fù)合焊、微束等離子焊、攪拌摩擦焊等在特定應(yīng)用場景下的潛力。 材料-工藝協(xié)同設(shè)計: 開發(fā)更易焊接、抗高溫氧化、低接觸電阻的雙極板材料及表面處理技術(shù)。 總而言之,燃料電池雙極板焊接是一門融合了材料科學、熱力學、機械精密制造與自動控制的綜合藝術(shù)。克服其技術(shù)挑戰(zhàn),實現(xiàn)高效、可靠、經(jīng)濟的精密連接,是推動燃料電池成本下降、性能提升和產(chǎn)業(yè)化進程的關(guān)鍵一環(huán)。每一次精準的焊縫,都在為清潔高效的氫能未來奠定堅實的基礎(chǔ)。
點擊右側(cè)按鈕,了解更多激光打標機報價方案。
免責聲明
本文內(nèi)容通過AI工具智能整合而成,僅供參考,博特激光不對內(nèi)容的真實、準確或完整作任何形式的承諾。如有任何問題或意見,您可以通過聯(lián)系1224598712@qq.com進行反饋,博特激光科技收到您的反饋后將及時答復(fù)和處理。